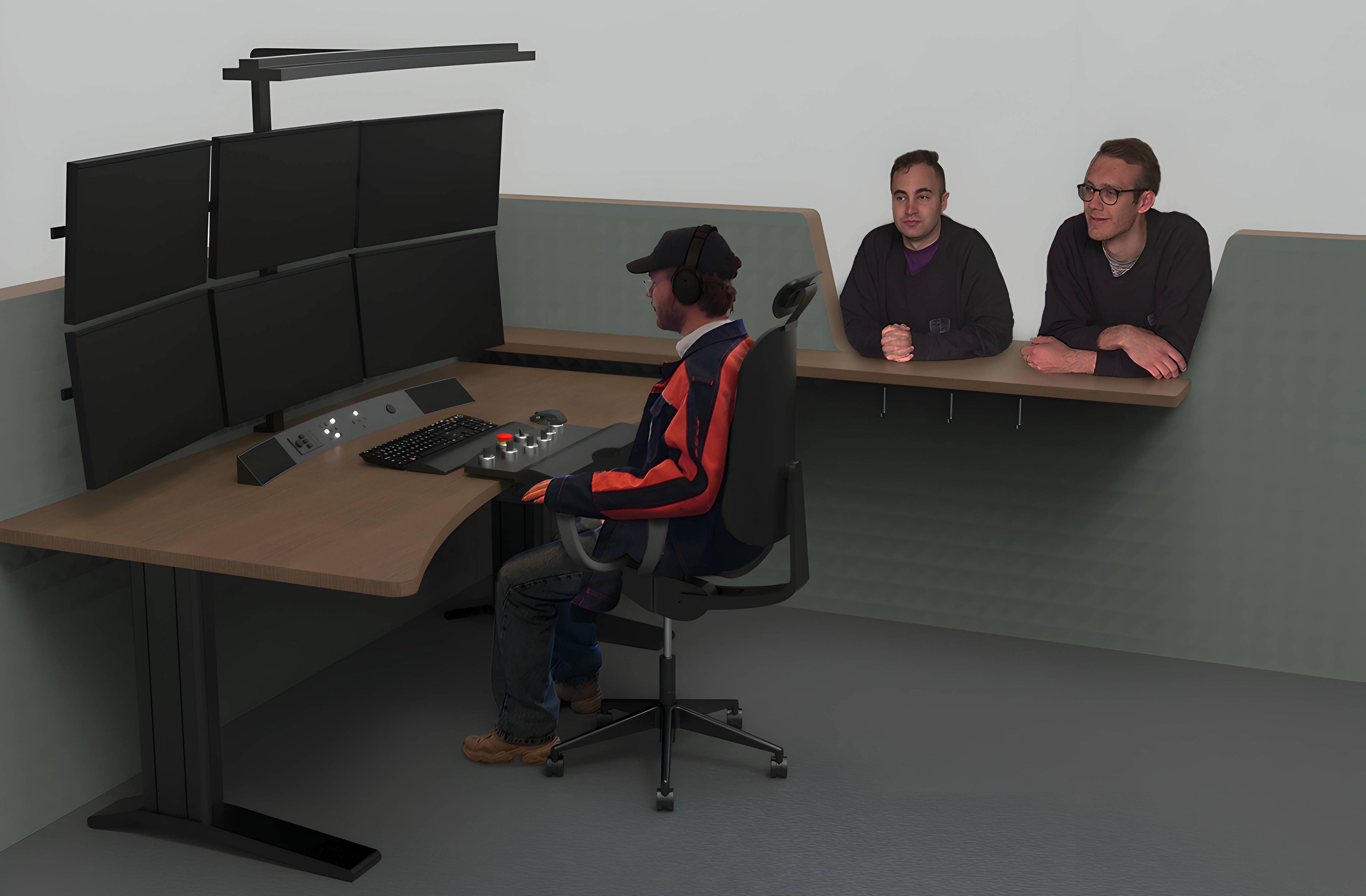
The Arc
Vargön Alloys, an alloy factory outside of the small town Vargön, decided to gather their previously scattered control rooms. The design studio Boid were hired to design the new centralized control room. As my bachelor thesis, I participated in the design of the work space of the melters, the person who controls the alloy furnaces. The goal was to create a workplace considering: Physical and cognitive ergonomics, Communication, Users attitude to the change & Safety hazards.
The Arc, is a social, professional, and modern workplace for the operators of the future. It displays the necessary information in one place, which allows the melter to monitor the furnace at all times and react to emergencies quickly. By keeping the controls the same, it avoids over digitizing the work environment of a user group who do not consider themselves to be very comfortable with modern technology.
- Images can be translated to English on request-
Type of project
Bachelor’s thesis project
Duration
5 Months (spring 2021)
Partner Companies
Boid, Vargön Alloys
Teammates
Gustav Dagberg, Saga Jilsén,
Jakob Kitzing, Mats Kullerstrand,
Linda Silberberg
Jakob Kitzing, Mats Kullerstrand,
Linda Silberberg
Methods & Tools
Interviews, Observation, HTA,
KJ-analysis, List of requirements, Morphological matrix, Prototyping, Fusion 360
KJ-analysis, List of requirements, Morphological matrix, Prototyping, Fusion 360

Project planning
The project was divided into four phases: 1. Start, 2. Data gathering & analysis, 3. Ideation, conceptualization and evaluation, & 4. Visualisation.
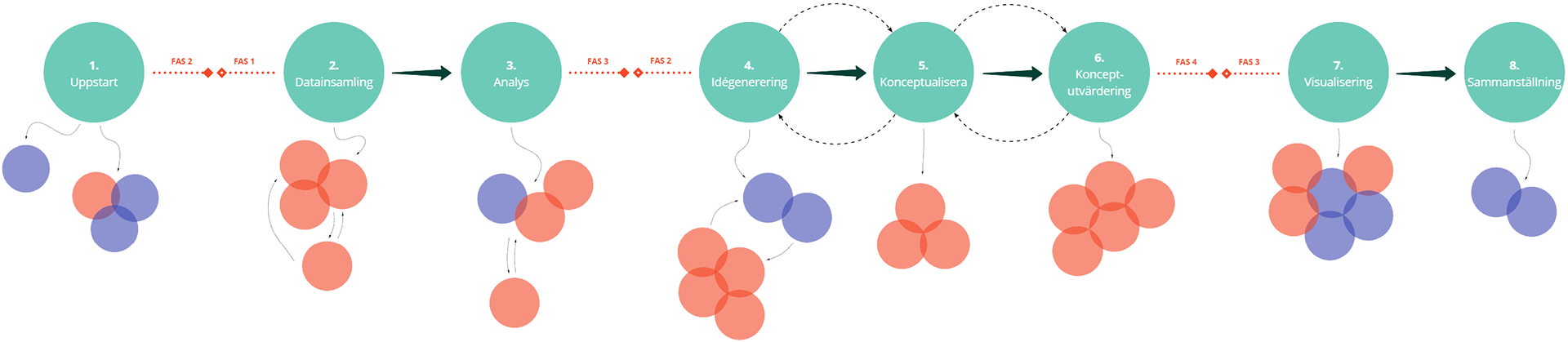
Phase 1 - Start
During the start of the project, the bachelor group got to partake in the previous work done by BOID, got introduced to the situation by Vargön Alloys, and discussed expectations of deliverables.
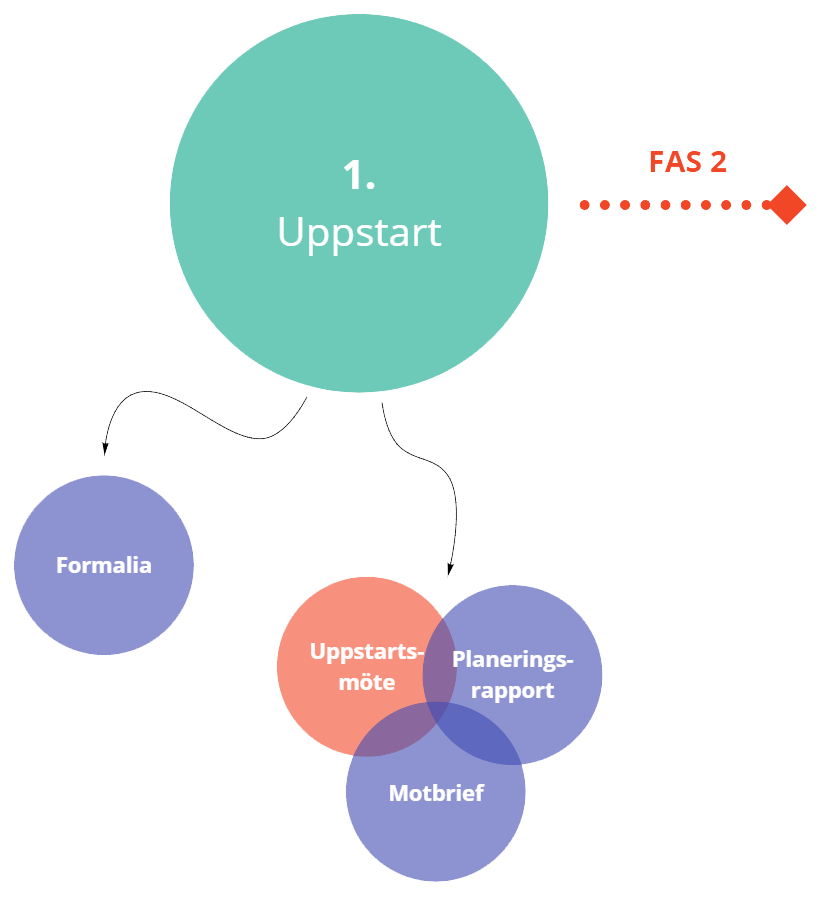
Vargön Alloys - Alloy industry
Today, there are four different control rooms at Vargön Alloys. In each of them, the furnace is controlled from the melting chair. As the different melters, the person who controls furnace, are spread out in different parts of the factory, communication and teamwork between them is impossible. The best before date of the technology and design of the control rooms are to expire, and because of this Vargön Alloys are evaluating the options to create a centralized control room from where all of the furnaces are controlled. Vargön Alloys's vision of this new control room is that it would increase teamwork and communication throughout the factory, resulting in more efficient work as well as a better workplace for the employees. Our role in the project was to design the work space of the melters in the new control room.
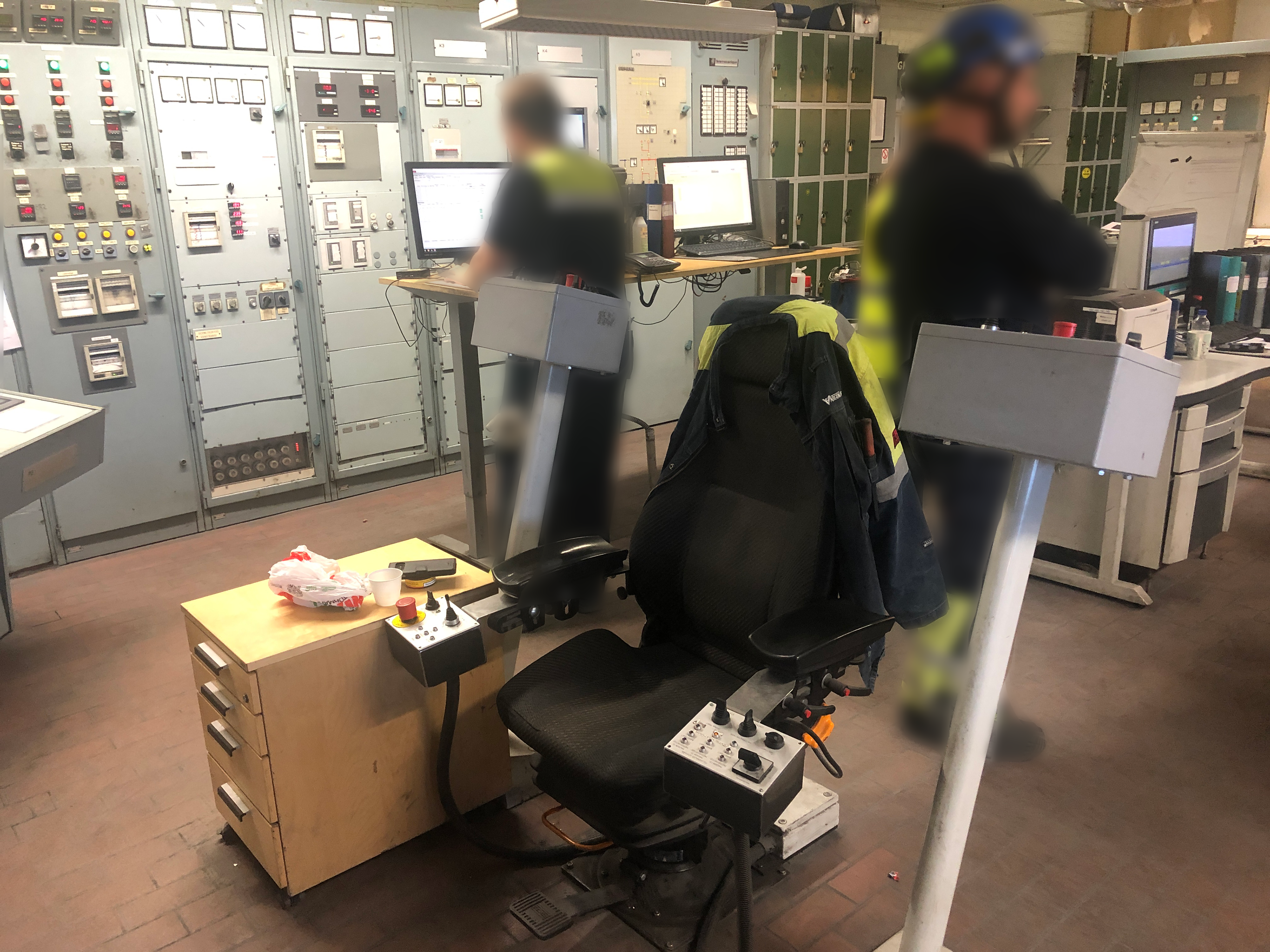
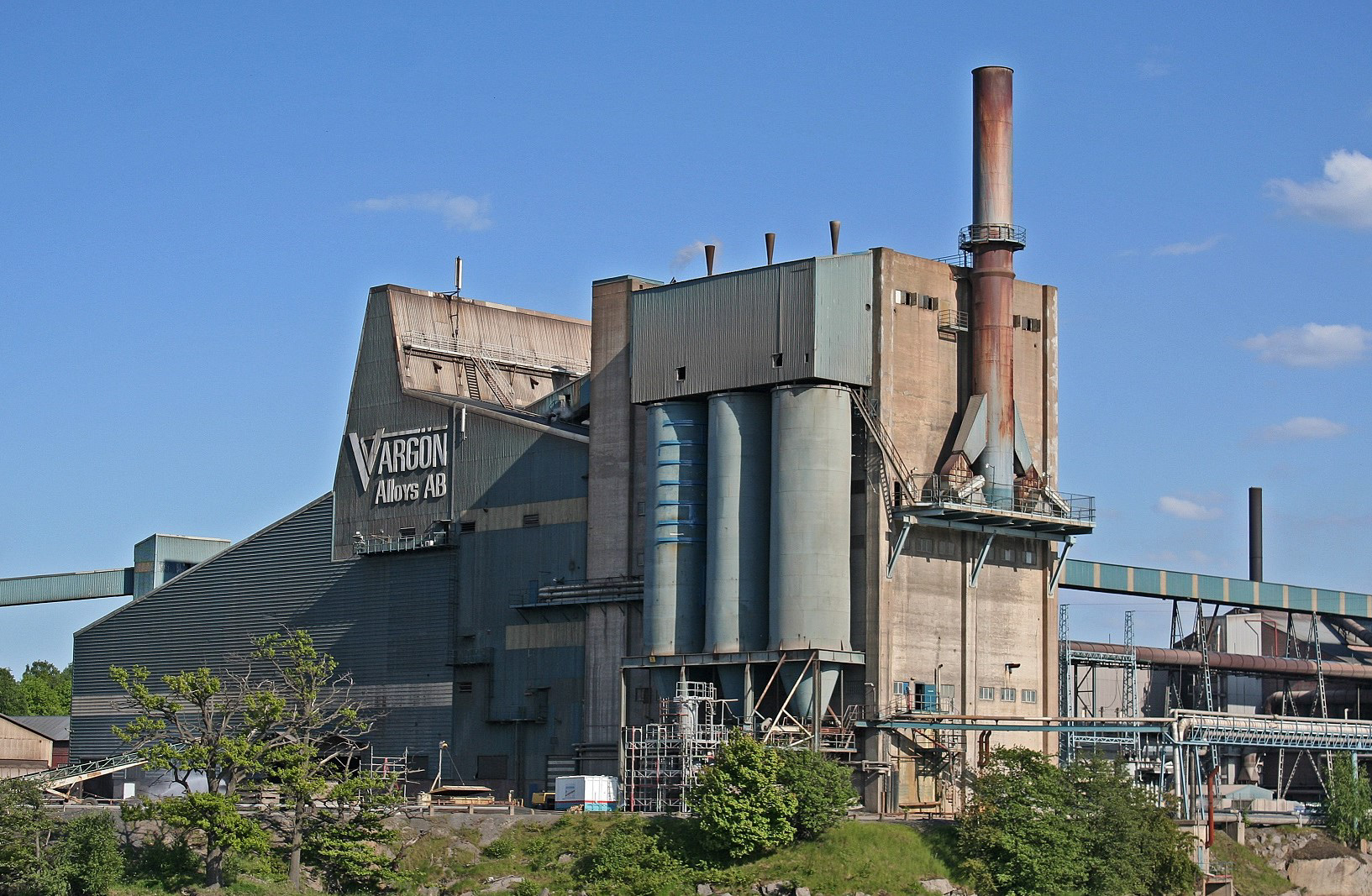
Phase 2: Data gathering & analysis
During the data gathering and analysis phase, literature studies and market analysis were done of control room environments as a base for the future design choices. A remote tour of the factory were given, and interviews with workers were conducted. An HTA and KJ-analysis were then used to analyze the data, which were formulated into a list of requirements.
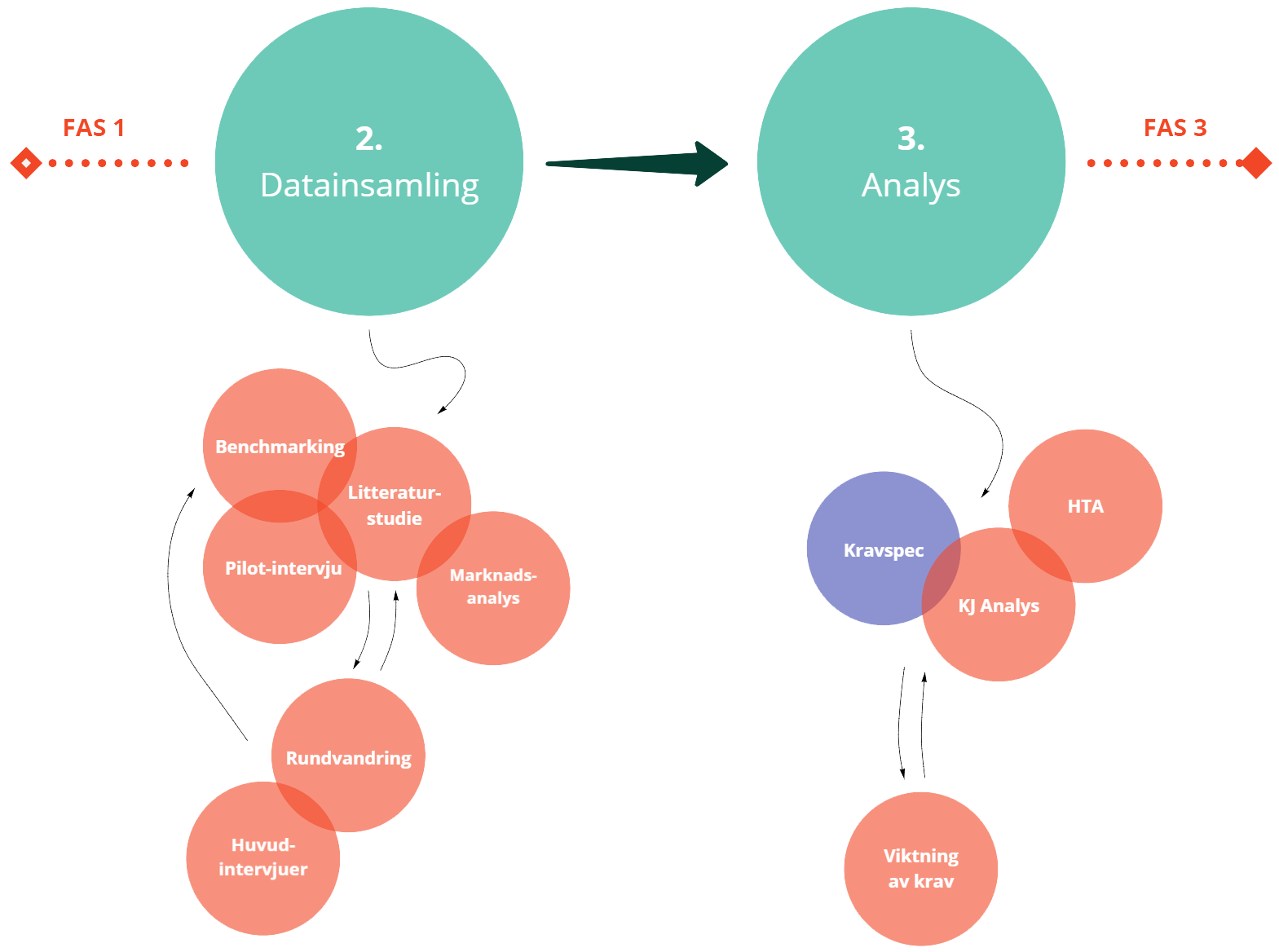
Work duties of a melter
The melter spends the majority of his work day in the melters chair, where monitors the furnaces temperature, status and controls the feeding and tapping machines. Occasionally, the melter walks away to log data parameters from the furnace. During this time he is unable to see the monitoring cameras. There are also other workers present in the control room which are involved in the tapping of molten alloy, and other logistic duties. Communication between these work roles is key. The melter needs to be present at all time, and needs to be covered by a coworkers during toilet breaks. Lunch is often eaten in the melter chair due to this factor.
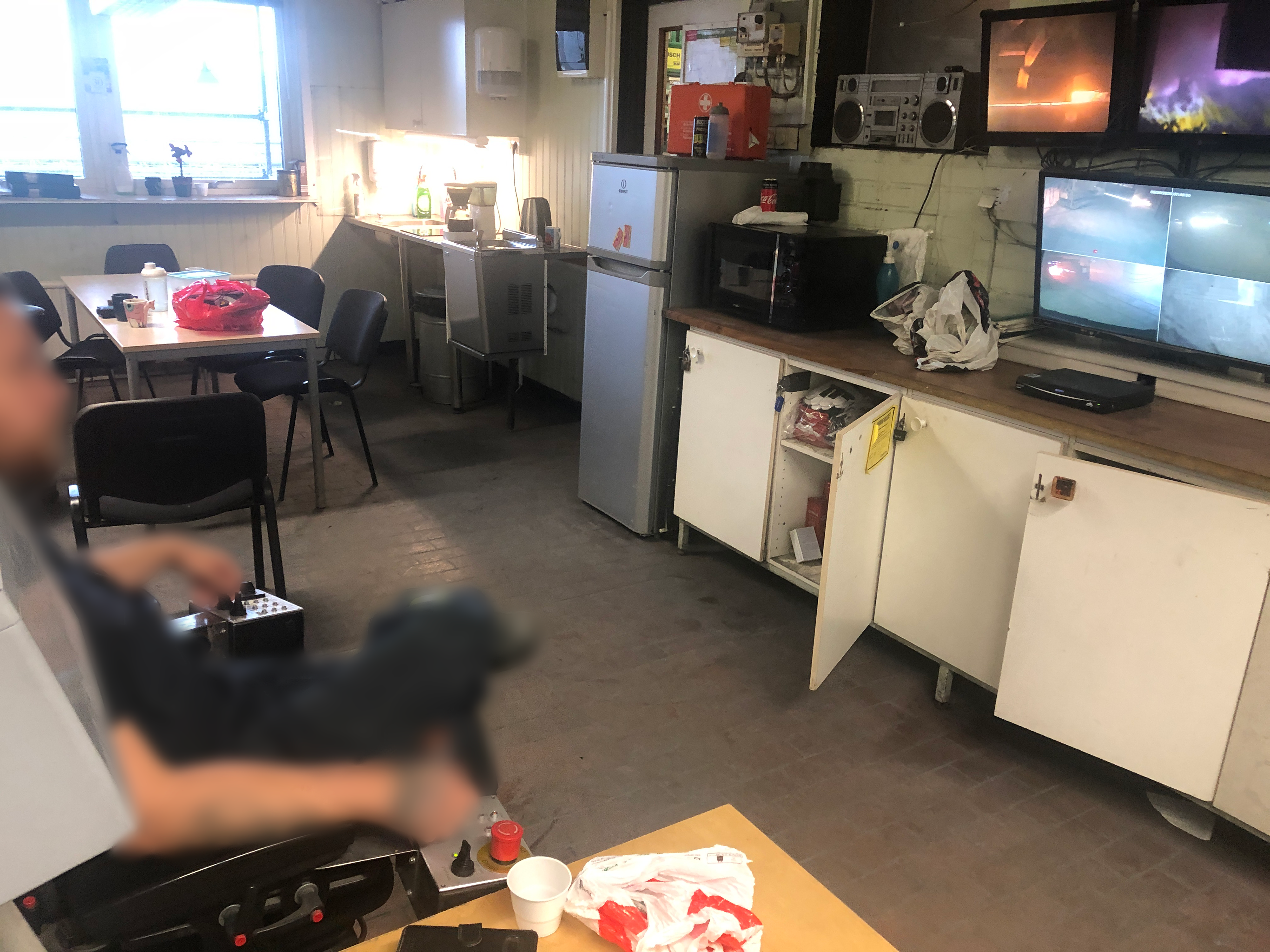
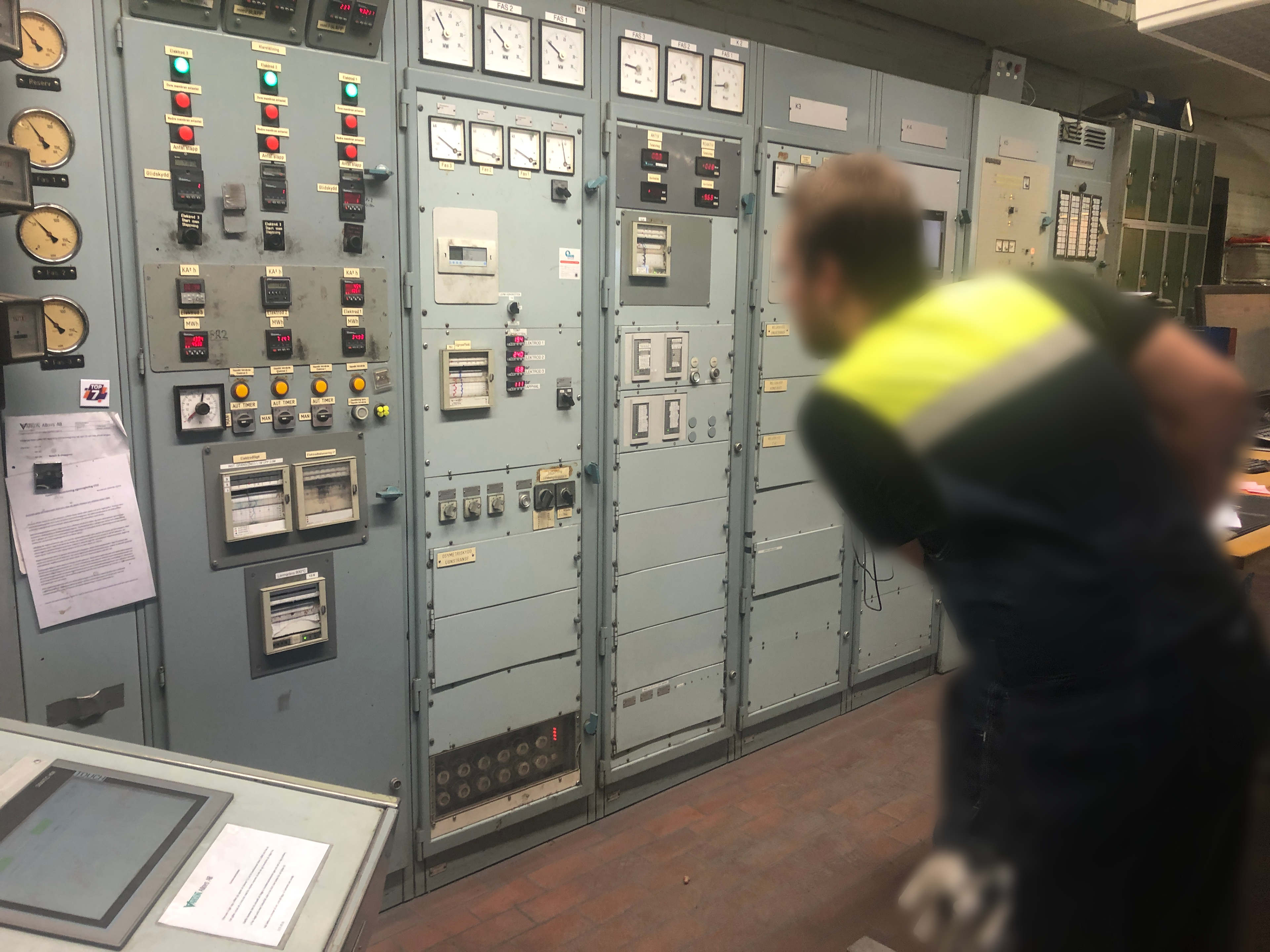
Controlling the furnace
Due to the limitations of working remote, the design team did not get the opportunity to test the feeding controls of the melter's chair. To better get a better feel for the user's work tasks, the controls were noted from the remote observation, and later recreated visually and physically prototyped.
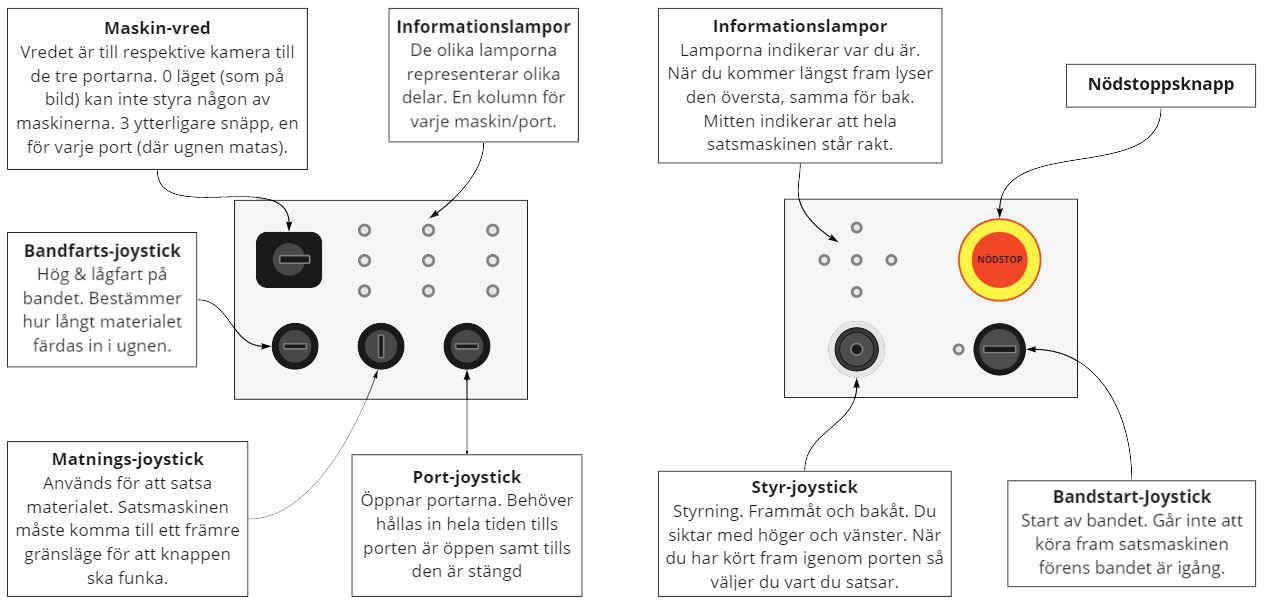
Phase 3 - Ideation, conceptualization and evaluation
After the analyze phase, ideation were done through brainstorming, speed-drawing and braindrawing. Partial solutions formed into concepts through a morphological matrix, and from there further refined. Three major concepts were created, which were evaluated during feedback sessions with melters. Rapid prototypes were made to give the design team a better understanding of the space and feel of partial solutions.
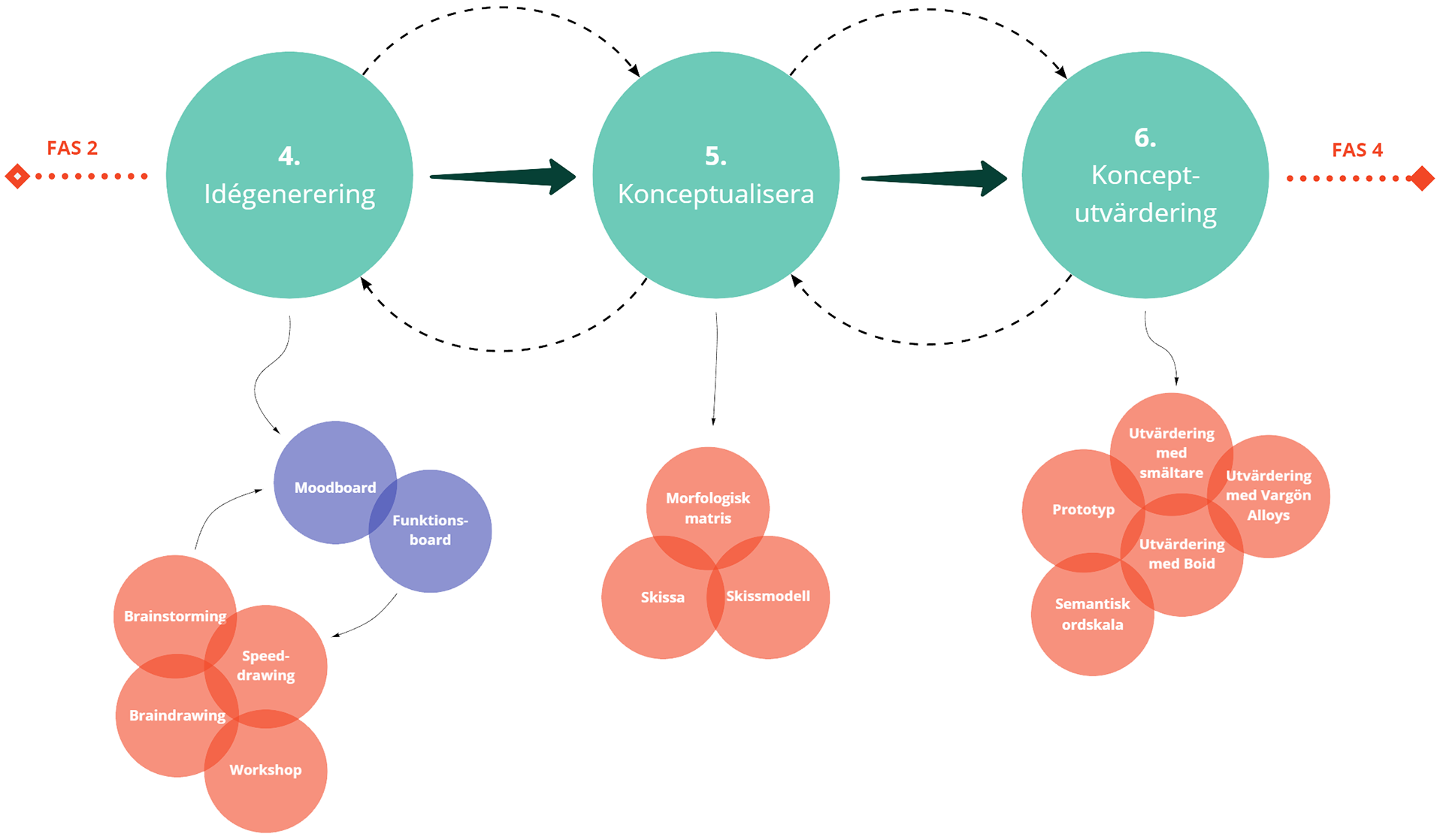
Concept A - Focus on communication
Coworkers of the melter that works close to the furnace gather metal dust which constantly covers the current control rooms, despite daily cleaning. A bar desk is located next to the work space, to limit the amount of dust transferred to the melters desk. In this concept, the feeding controls can be slid underneath the desk, to minimize their disturbance during other work tasks.
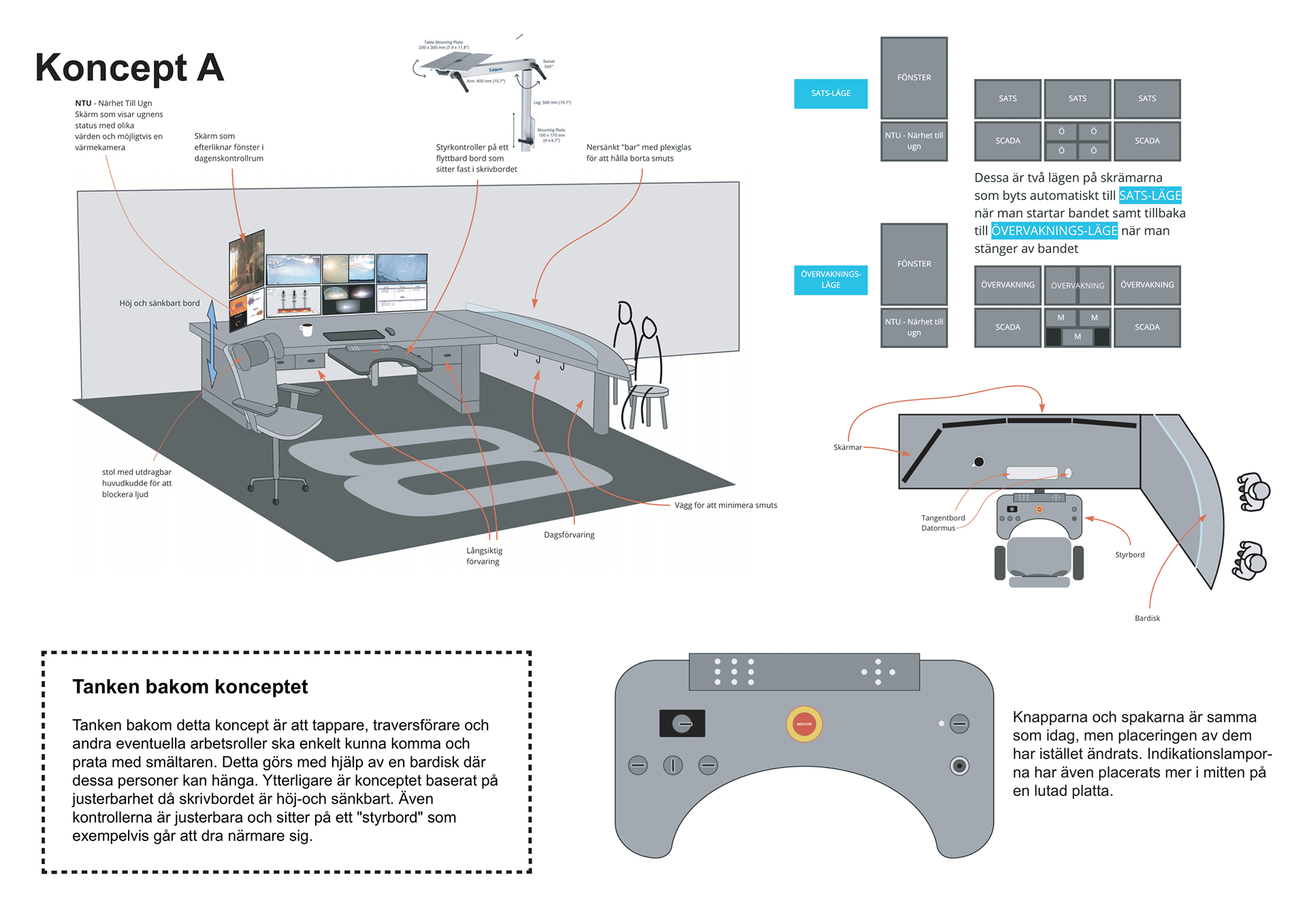
Concept B - Promoting movement
As the new centralized control room risks making the melters job more static, this concept tries to facilitate movement between work tasks. The melter chair can not be moved, which makes the melter walk to log values at the computer, as well as to communicate with coworkers to the right.
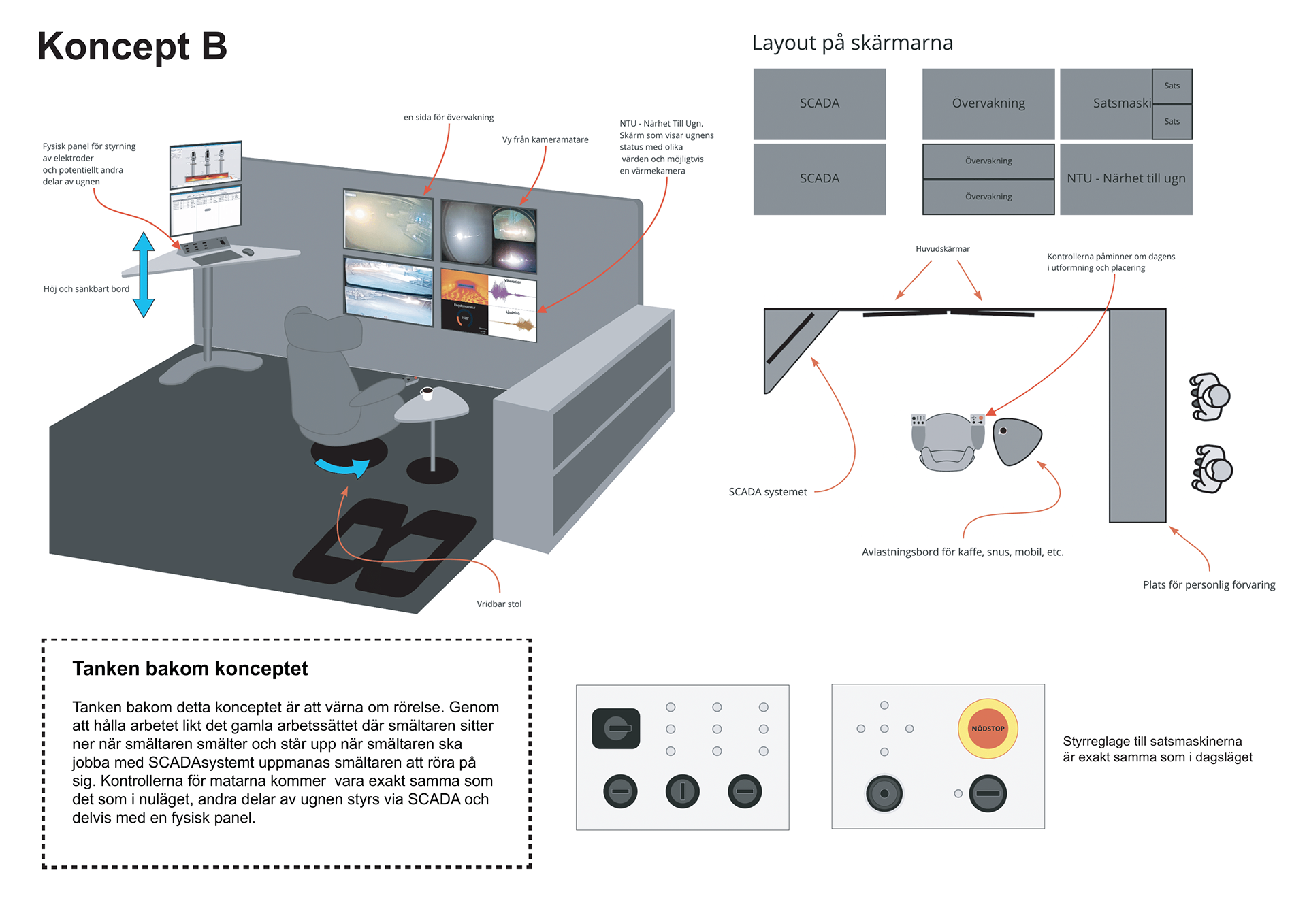
Concept C - Simplicity
In the new control room multiple melters will have their work spaces gathered. As this might result in it being crowded, this concept focuses on simplicity and minimizing the required space. The feeding controls and the keyboard are placed on opposite sides of a rotating slice of the desk, to be as space efficient as possible.
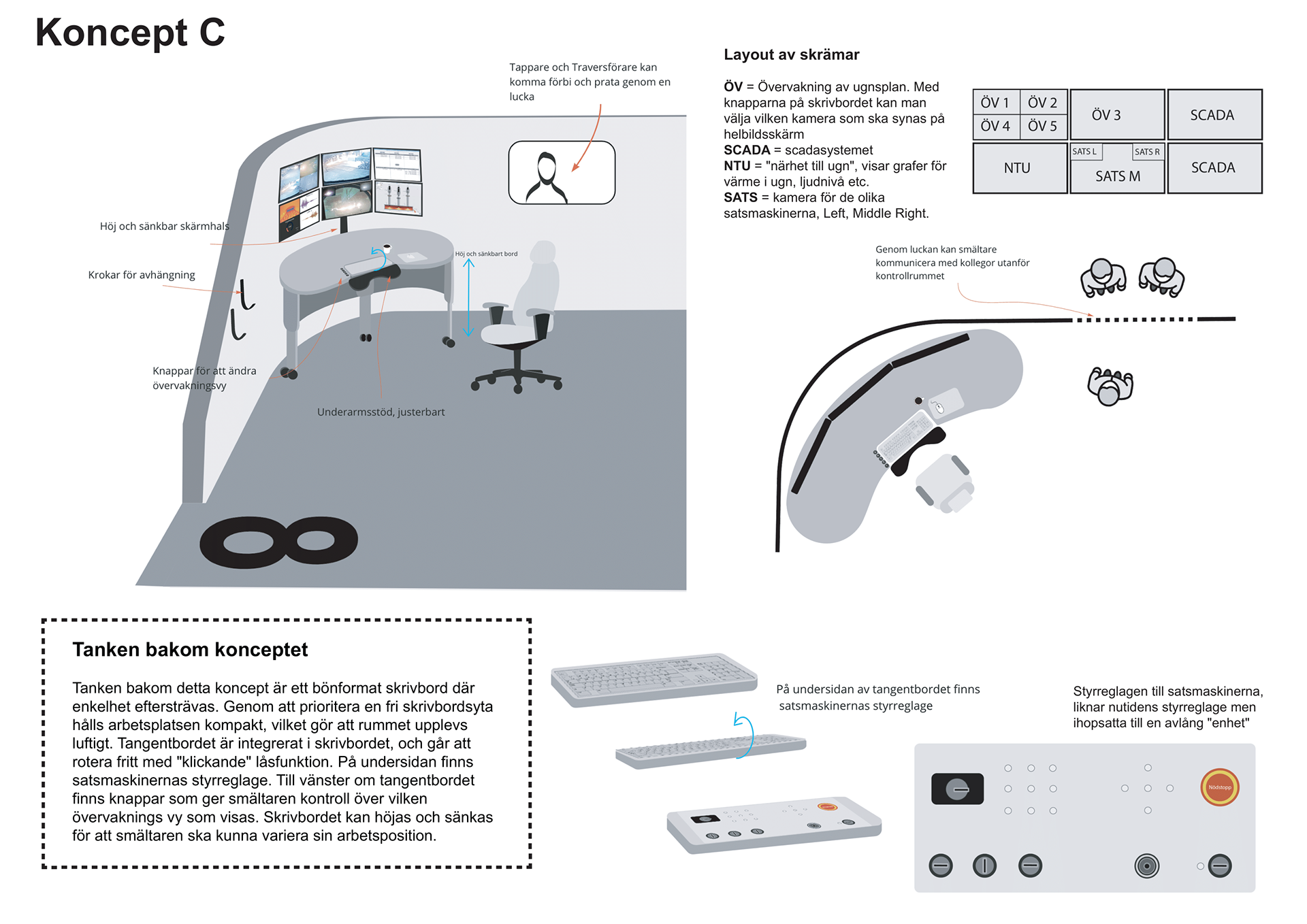
Prototyping - Ergonomics of controls
Rapid prototypes of the three concepts were made, to get a spatial understanding of how they would feel to the user. From this, the controls from concept A were further developed to be as comfortable and ergonomic as possible.
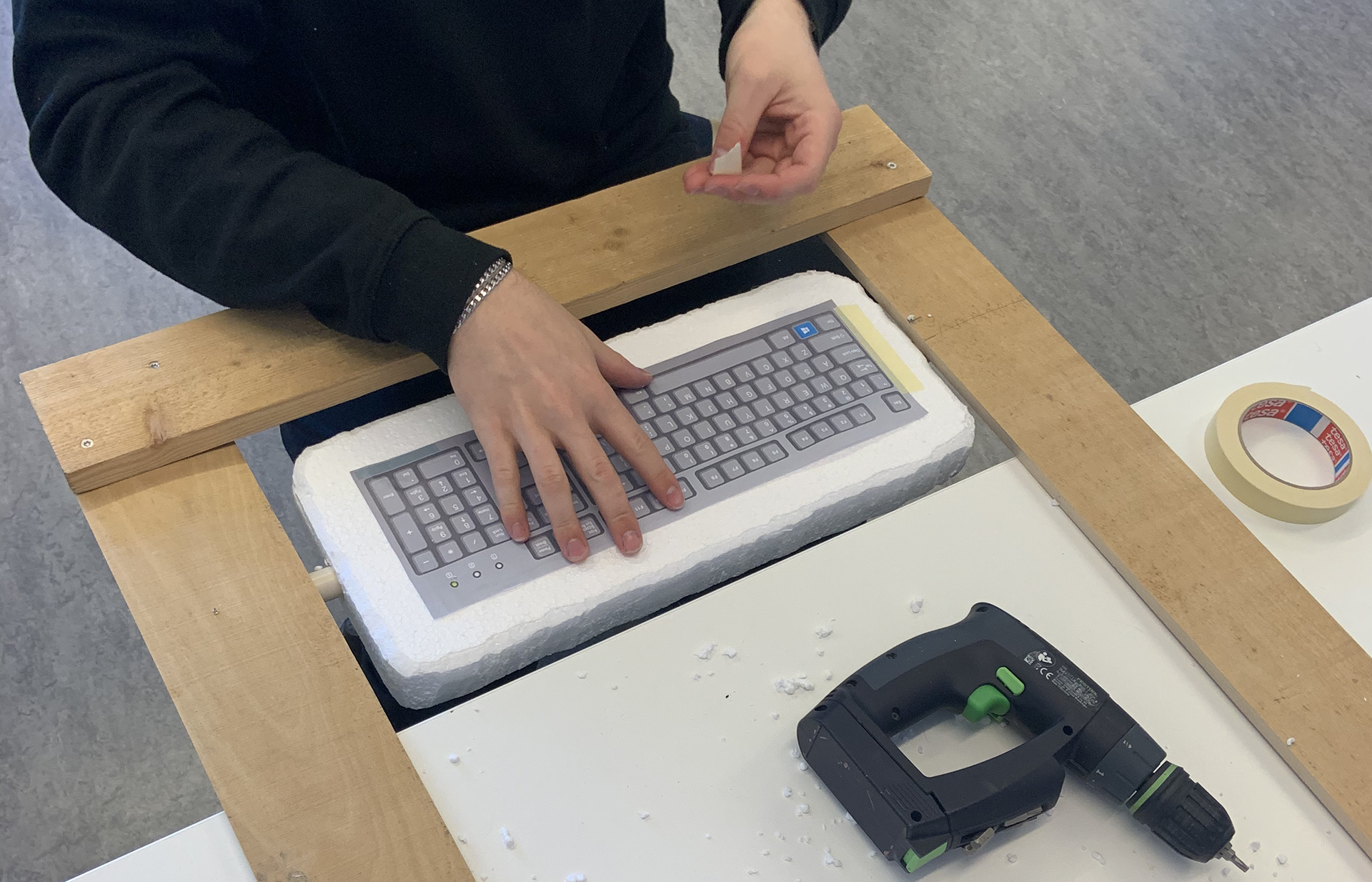
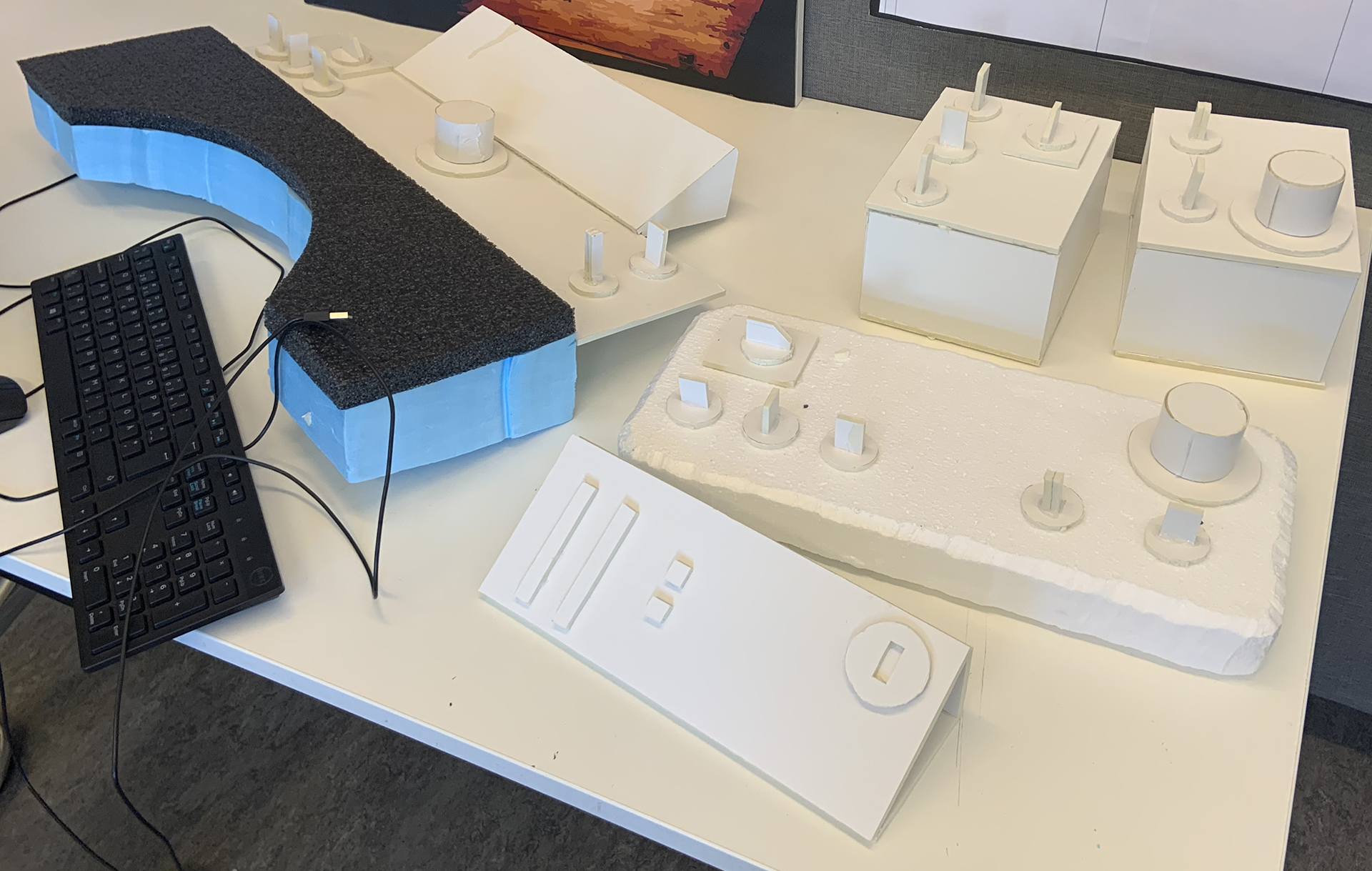
Prototyping - Cognitive ergonomics and visability
To evaluate what amount of information is overviewable, the number of screens, their size, information displayed, layout and the size of the desk were rapidly prototyped. Screenshots of concepts were printed, and tested in different formations and tried by people of varying heights.
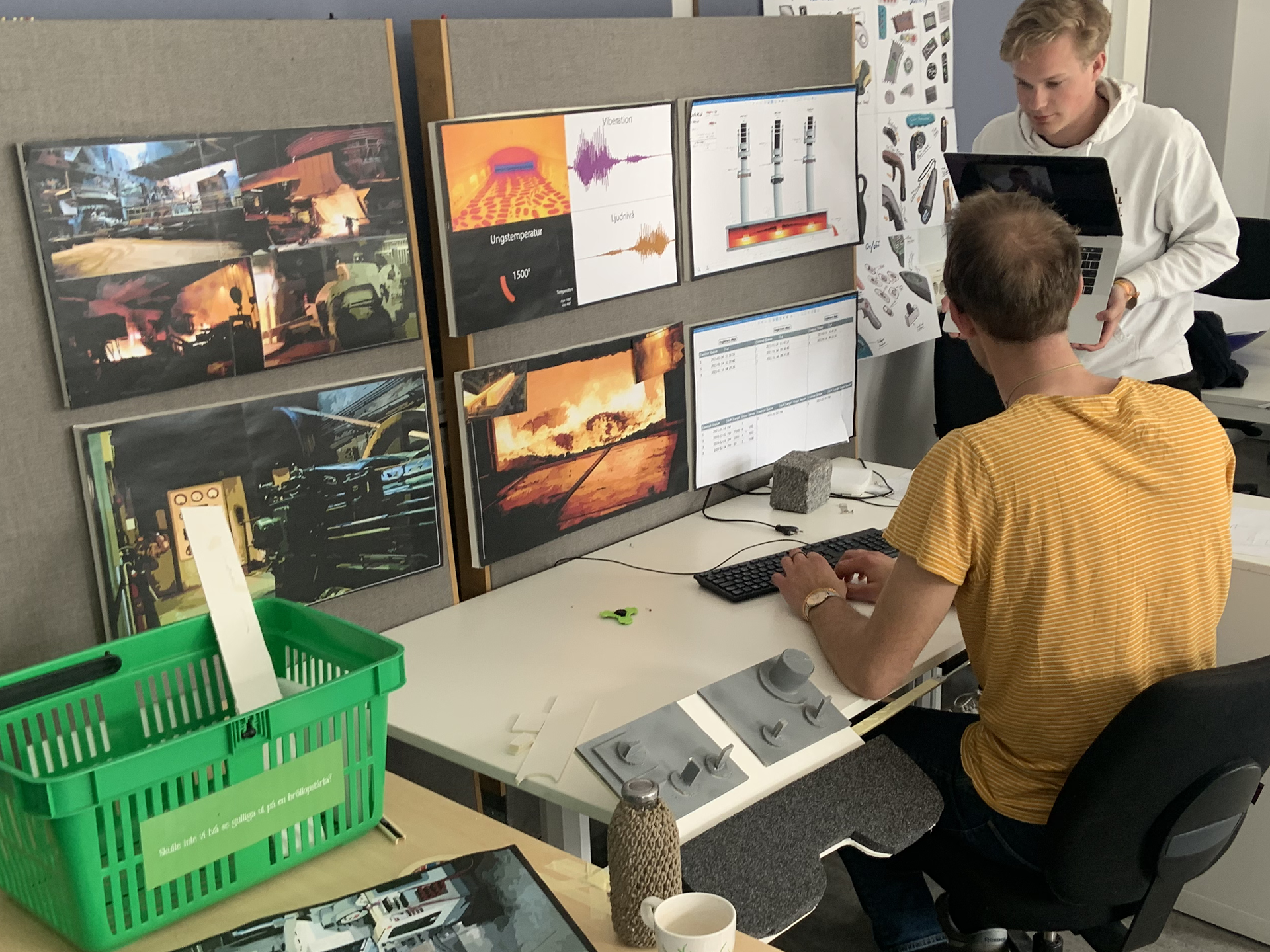
Phase 4: Visualisation
When the details of the final concept had been determined, the final concept were visualised through CAD in Fusion 360, and Photoshop.
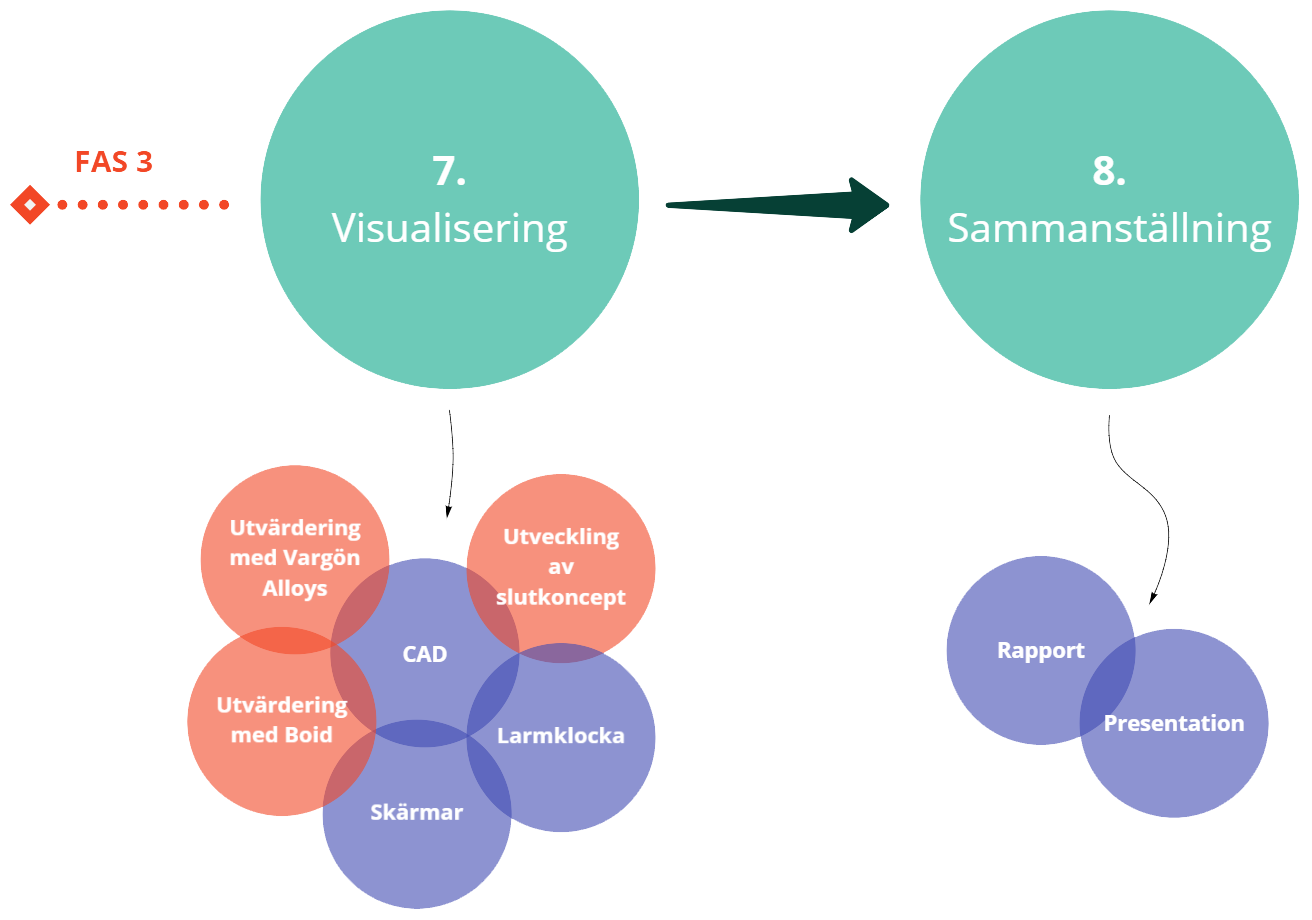
Final concept - The Arc
The Arc allows for constant monitoring, as the cameras of the furnace is always within the periphery independent of the current work task.
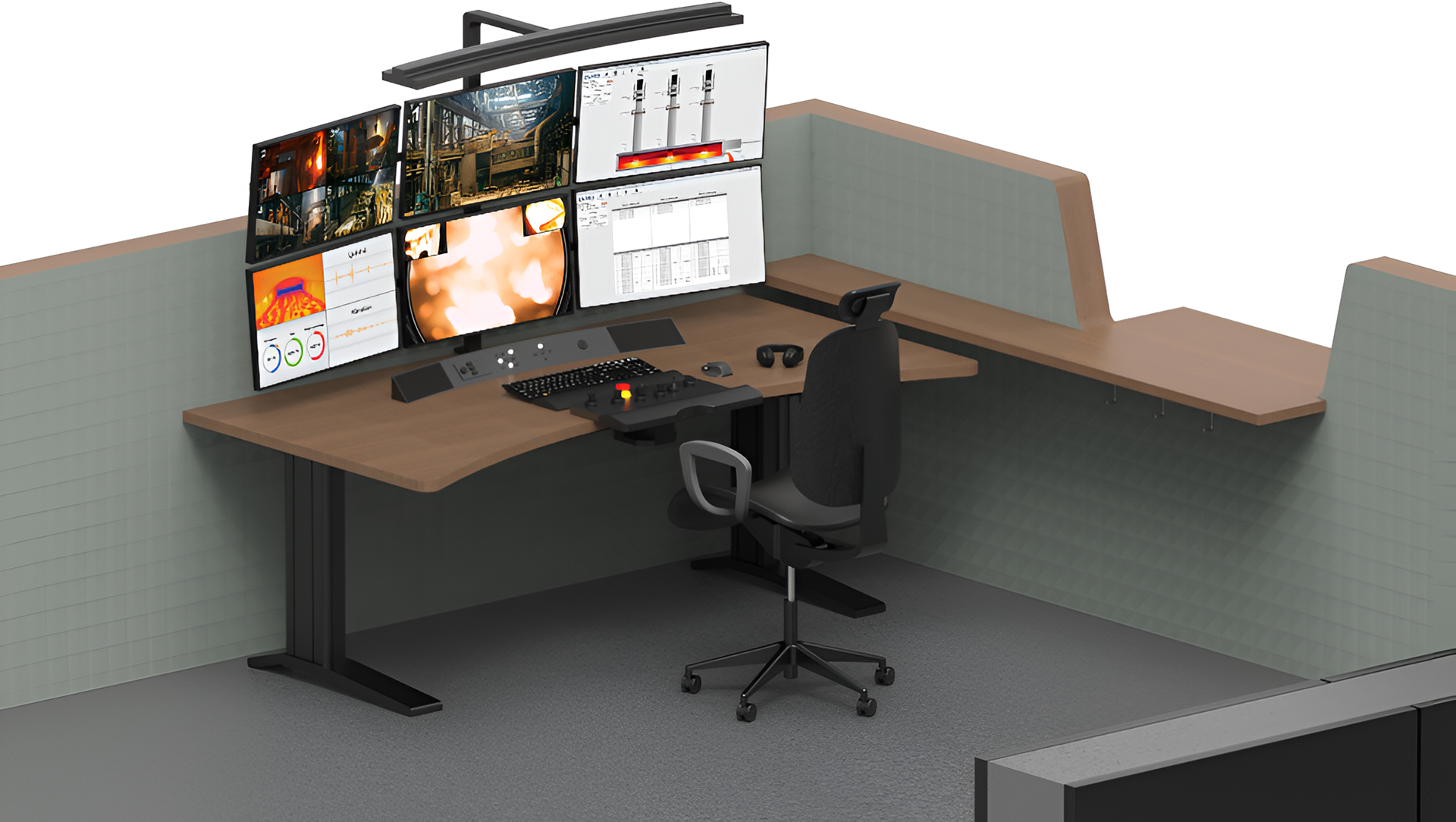
Teamwork
In the new control room, the melters are located next to each other for easy teamwork and communication. It also allows melters to take proper lunch and coffee breaks, which is something is not possible in the current control rooms.
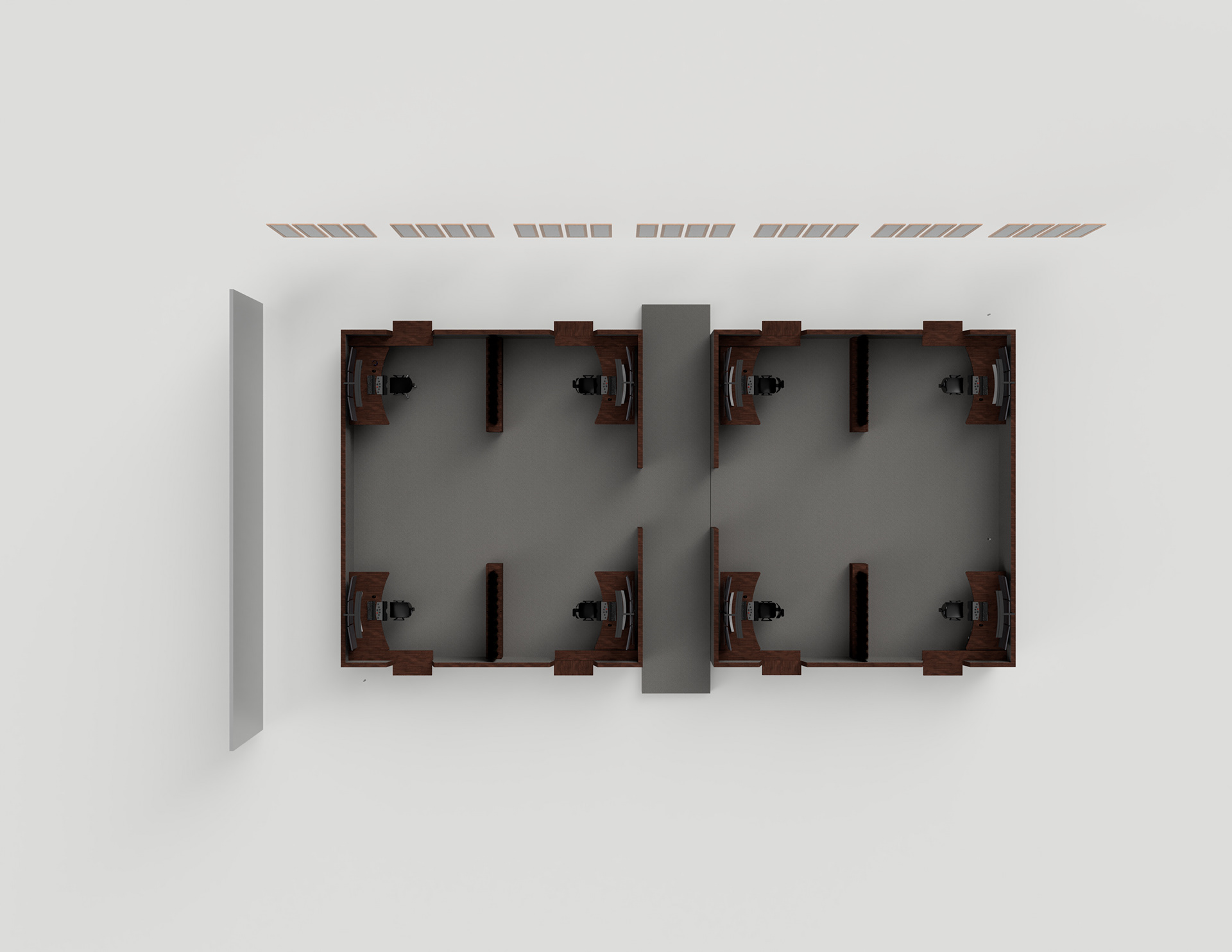
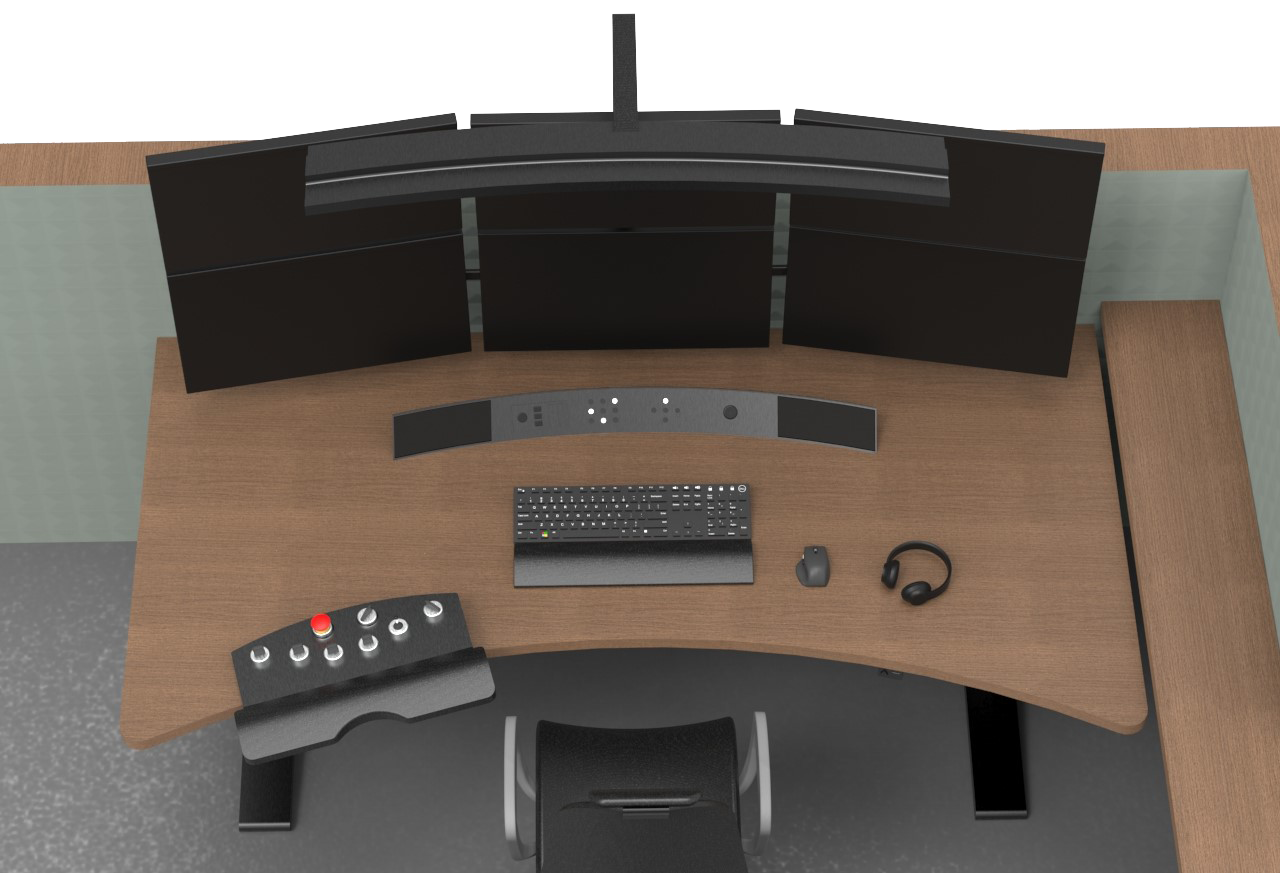
Desk & equipment
Each melters desk contain six screens, a sliding unit with the feeding controls, an alarm panel, a mouse, keyboard and headset. The desks height is adjustable to allow for both sitting and standing work. To improve the reach of the desk, there is a radial arc close to the user, giving the concept its name.
Alarm panel
When alarms are detected, the alarm panel begins with giving an visual signal through the LED-list. If not responded to withing 5 seconds, an audio signal is sent out through the speakers, alarming the rest of the melters.
The alarm panel also contains the indication lamps currently found on the feeding controls of the melter chair. This puts them in sight of the melter while looking at the screens.
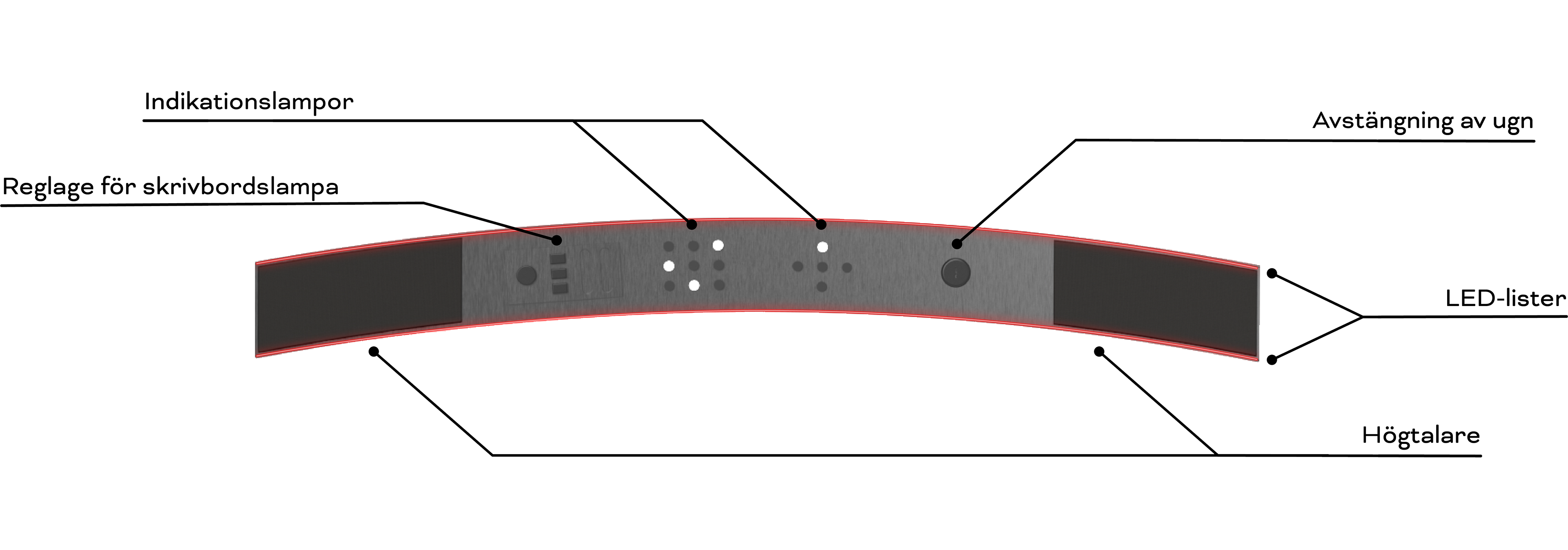
Alarms through smartwatch
If for some reason the alarm would not be responded to, a notification is also sent to a smartwatch of the melter. This keeps the melter responsible of the specific furnace in control of the situation, even if he has asked another melter cover for him during his break.
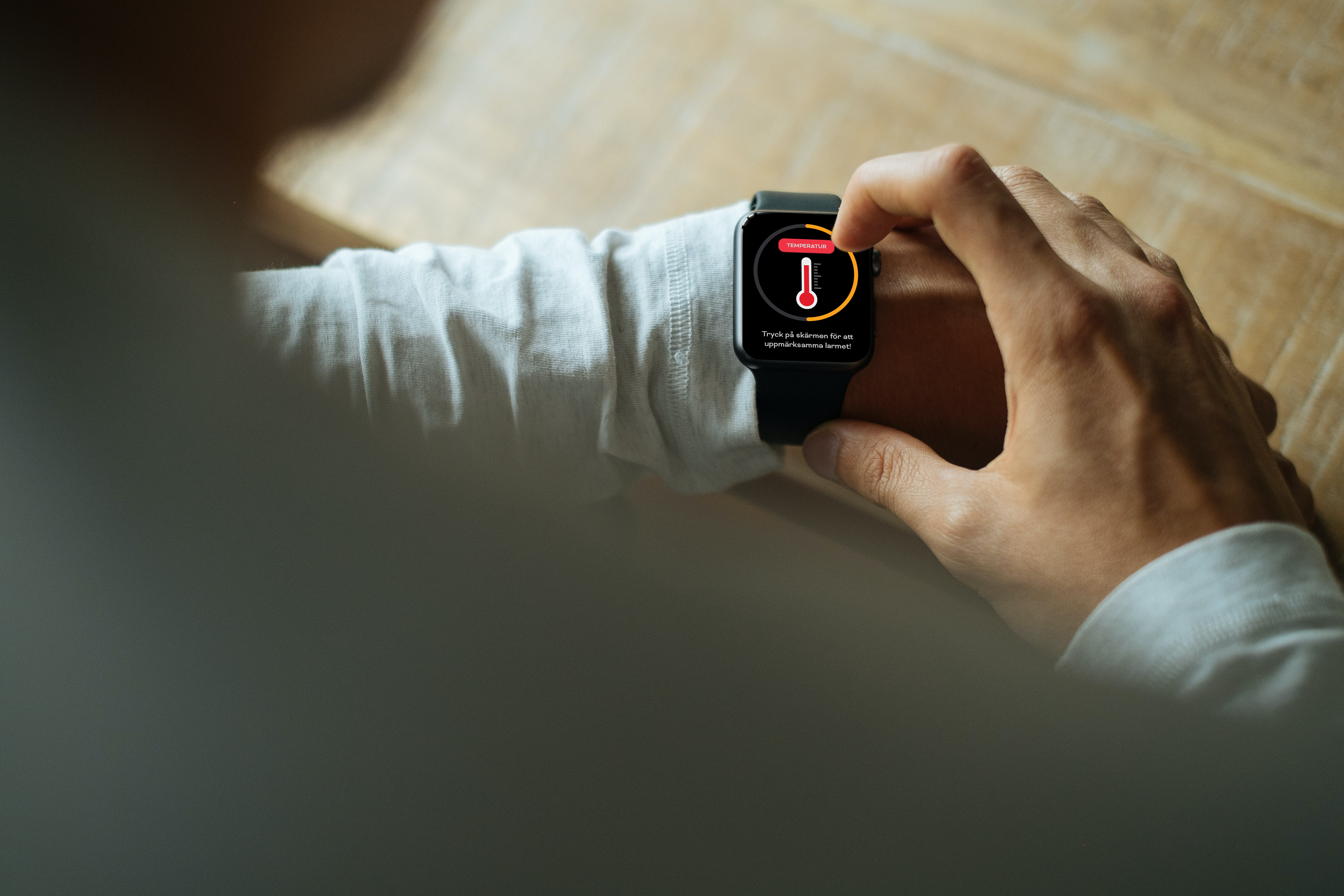
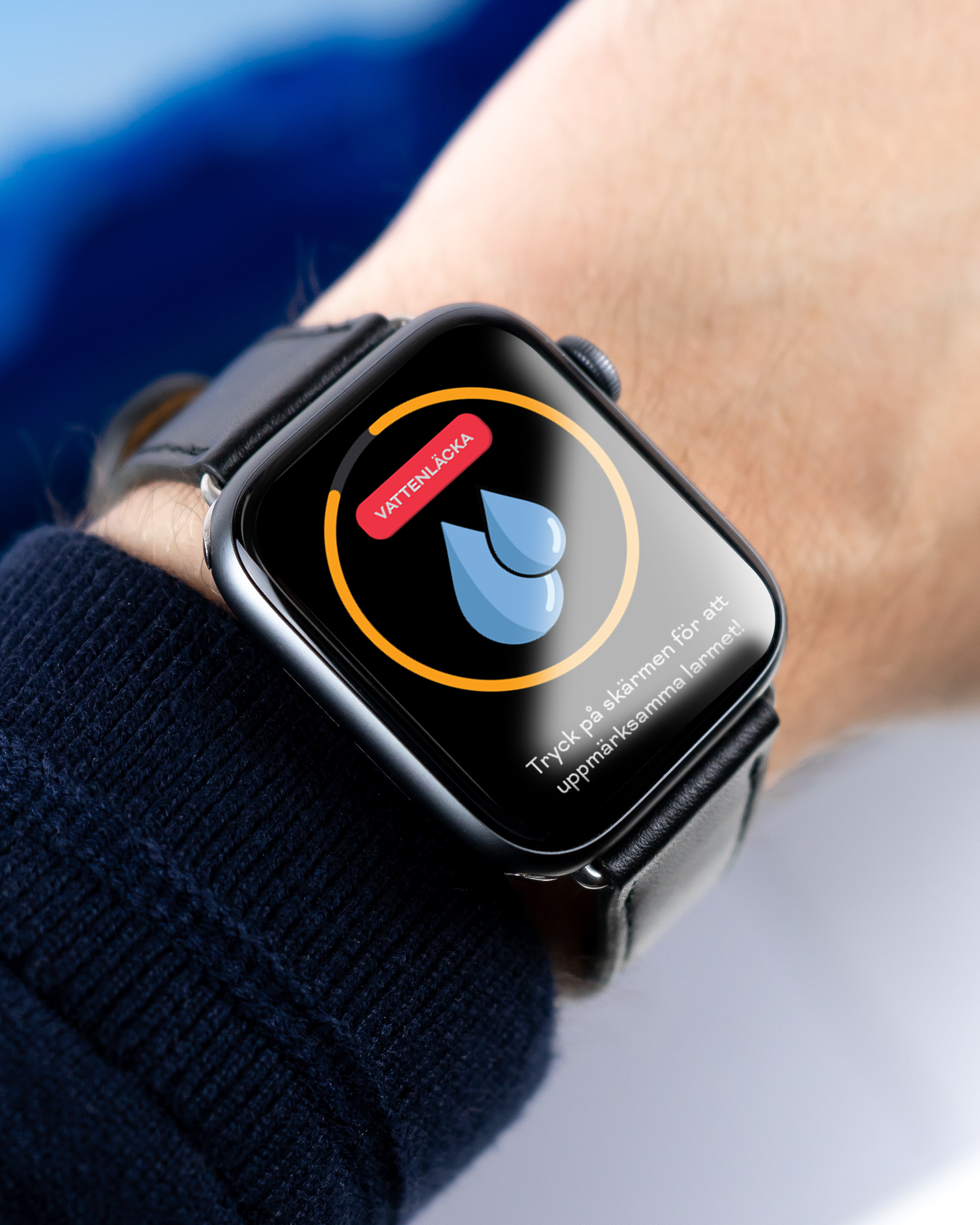
Feeding controls
The feeding controls of the furnace are located on a slidable unit at the desk. This allows the user to have them , while also putting them to the side when they are not in use.
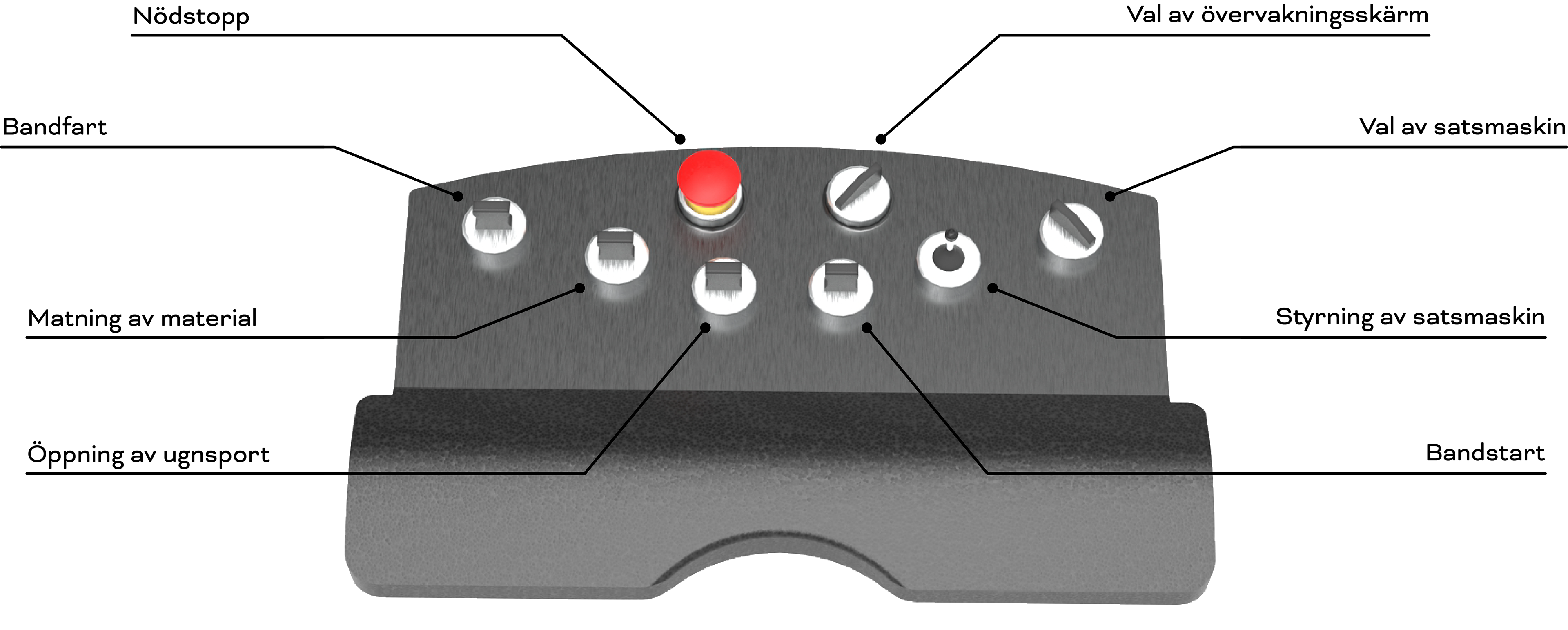
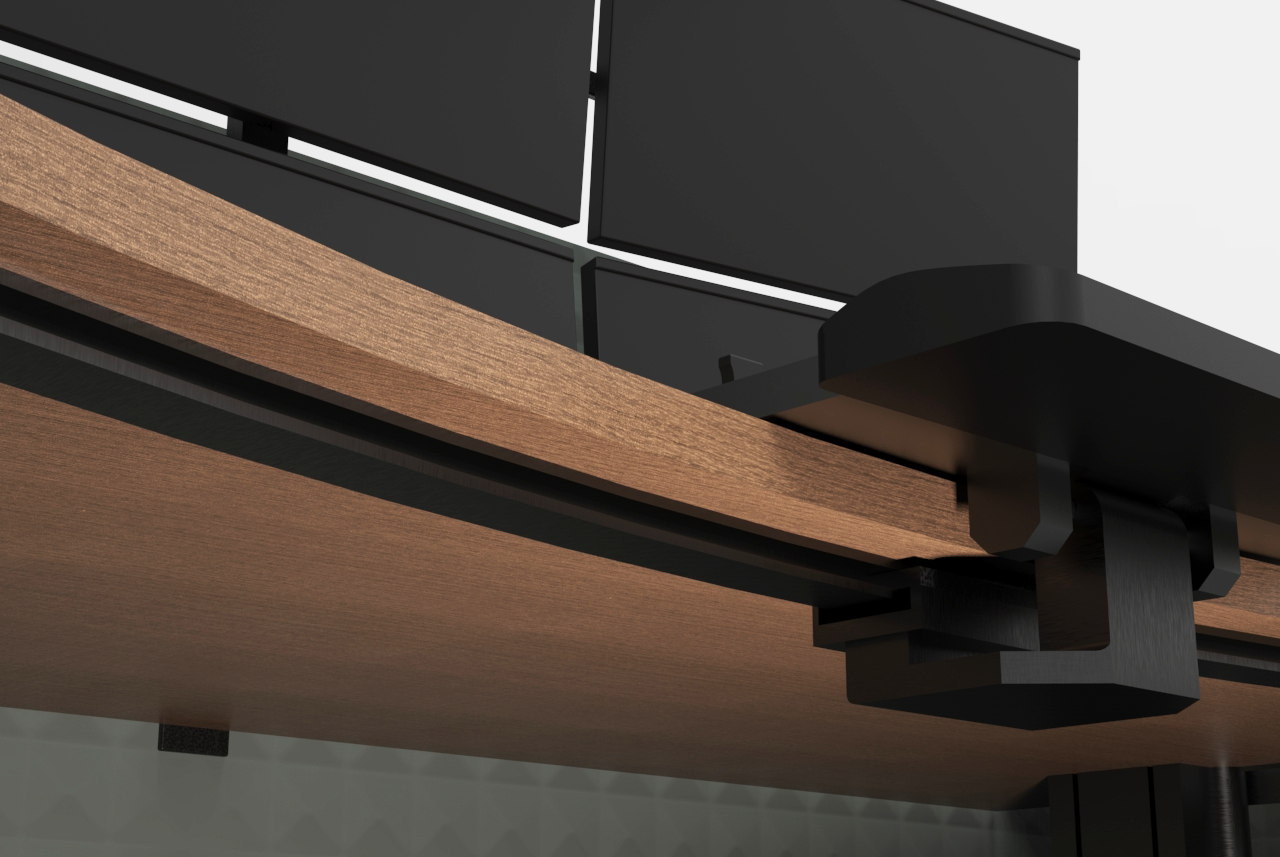
Adjusted for day- and night shifts
As production is constantly ongoing, the interfaces of the different systems come in both light and dark mode, and is automatically changed depending on the time of the day.
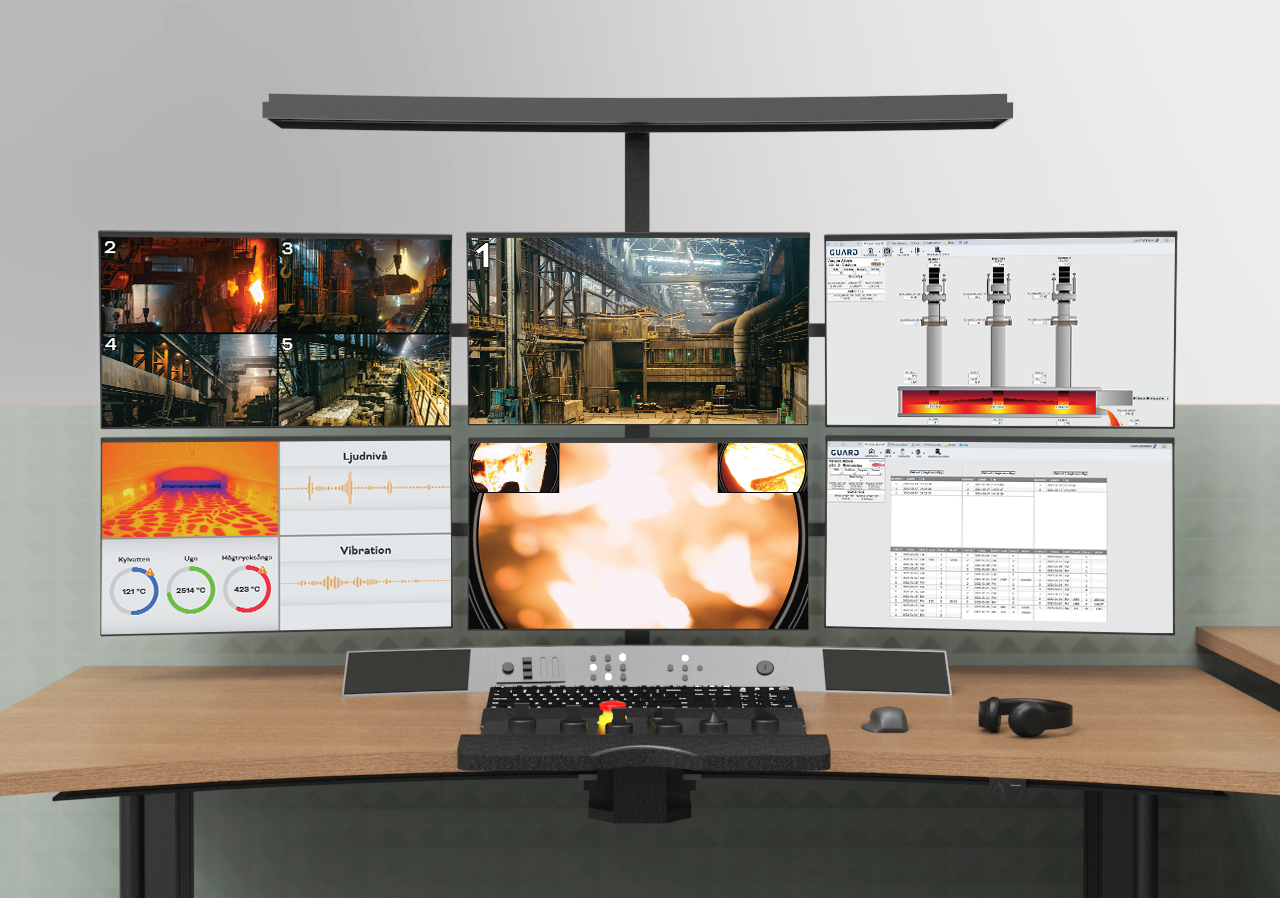
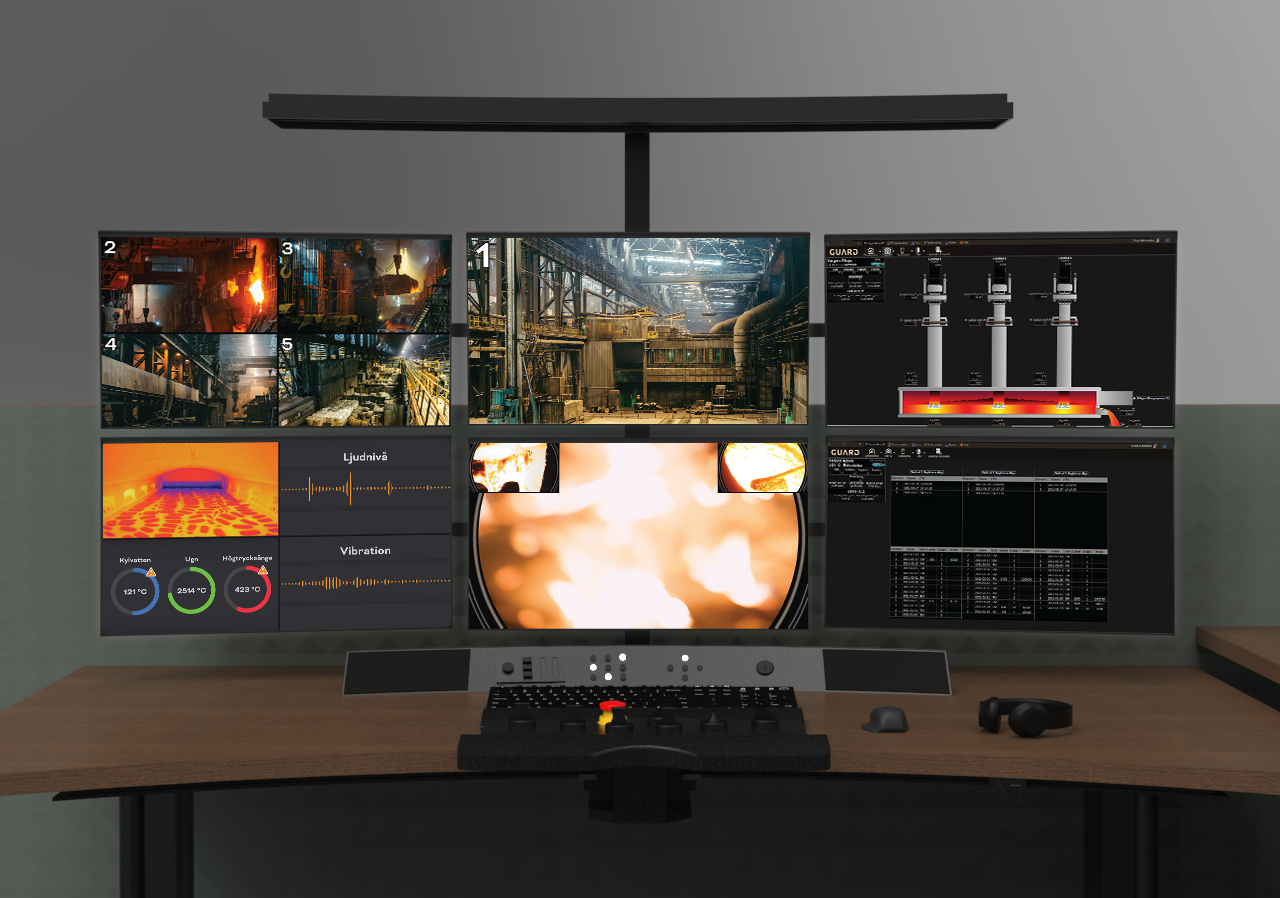
Communication with coworkers
While communication between melters are improved with a new centralized control room, there is a risk of losing the communication with the other coworkers of the same furnace. The bar desk next to the melter is a designated place to come and plan the next tapping of molten alloy, or have a quick chat.
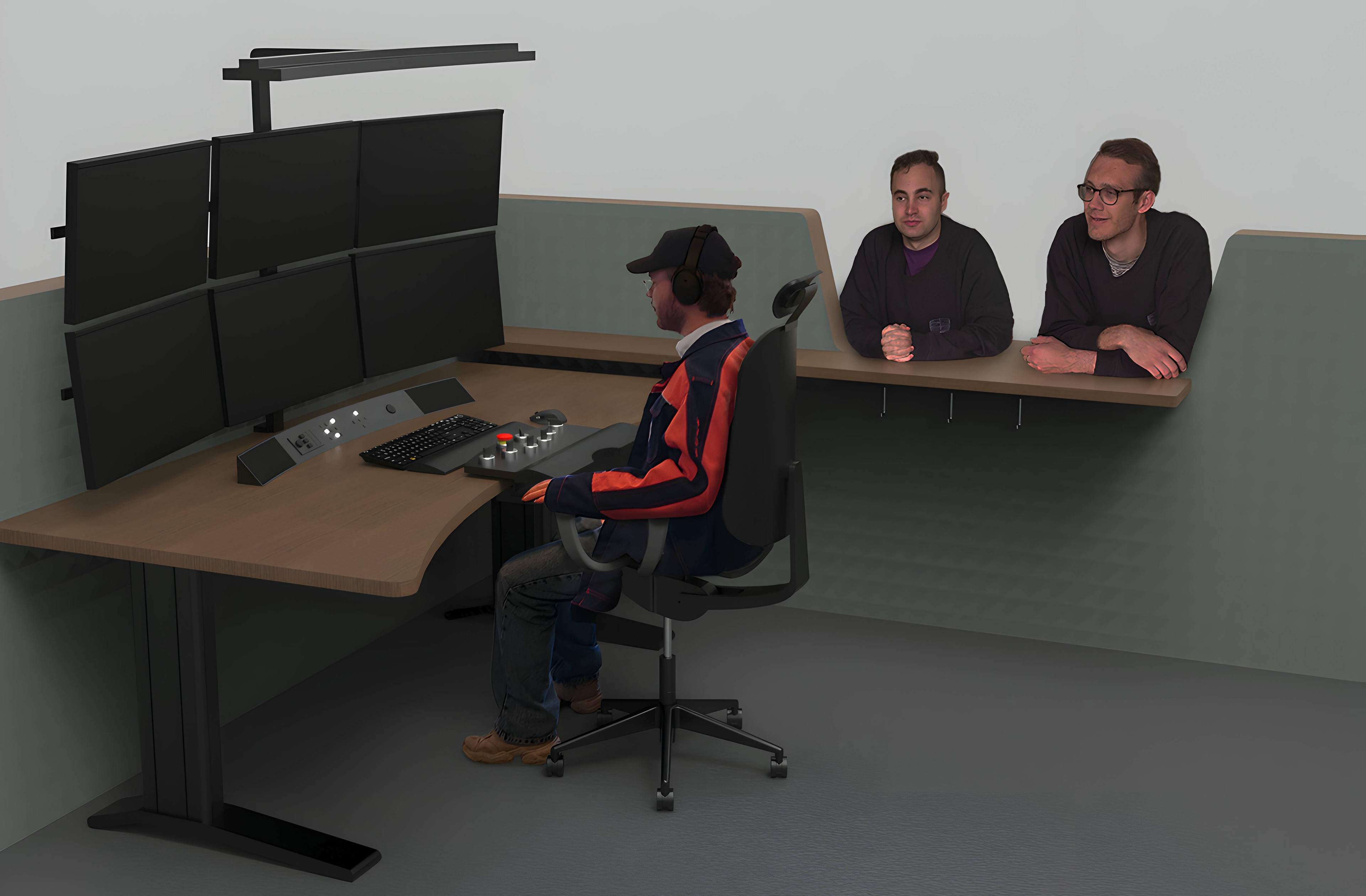
Acquired knowledge
Working as a group of six people for an entire semester requires more than just doing the work necessary. Clear communication, discussing expectations, and being able to have fun during coffee breaks improves both the mood of the group, and end result.
As this project was done during the covid-19 pandemic, all user studies were conducted remotely. By keeping a positive attitude, and being creative in our methods of data gathering, the group were still able to provide a solution for a usergroup we had never met, in an environment we had never been at. While it felt changeling at times, I believe this experience thought me a lot about how i can gain the perspective of the user when traditional means are not possible.